Facilities and Equipment
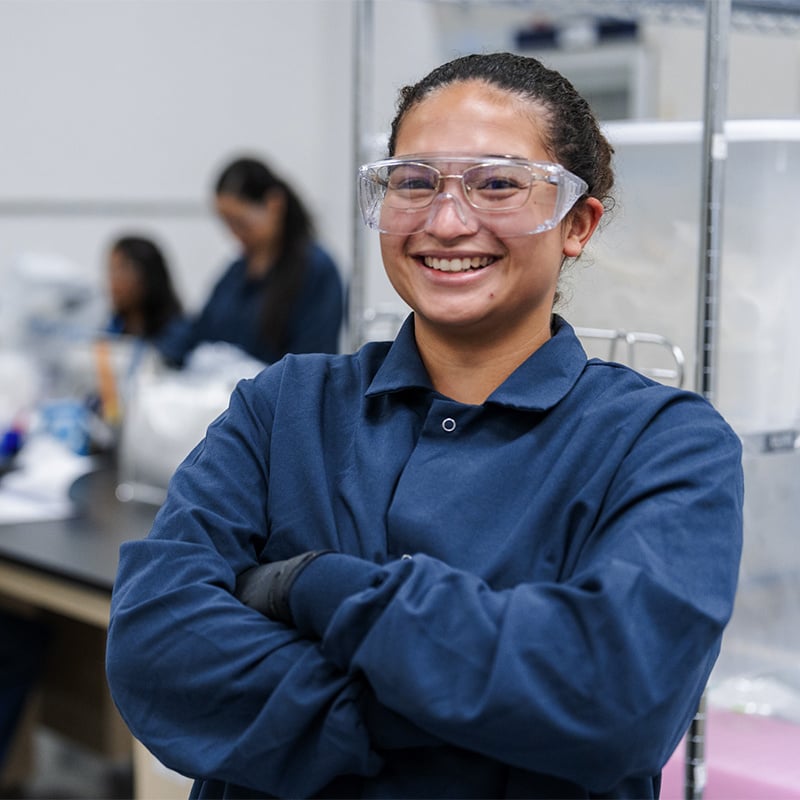
FDA-registered fill-finish site
- 20,000 sq. ft. facility
- Just-in-time warehousing and production
- Comprehensive mixing and compounding
- Single-use and dedicated reusable systems
- Aseptic filling
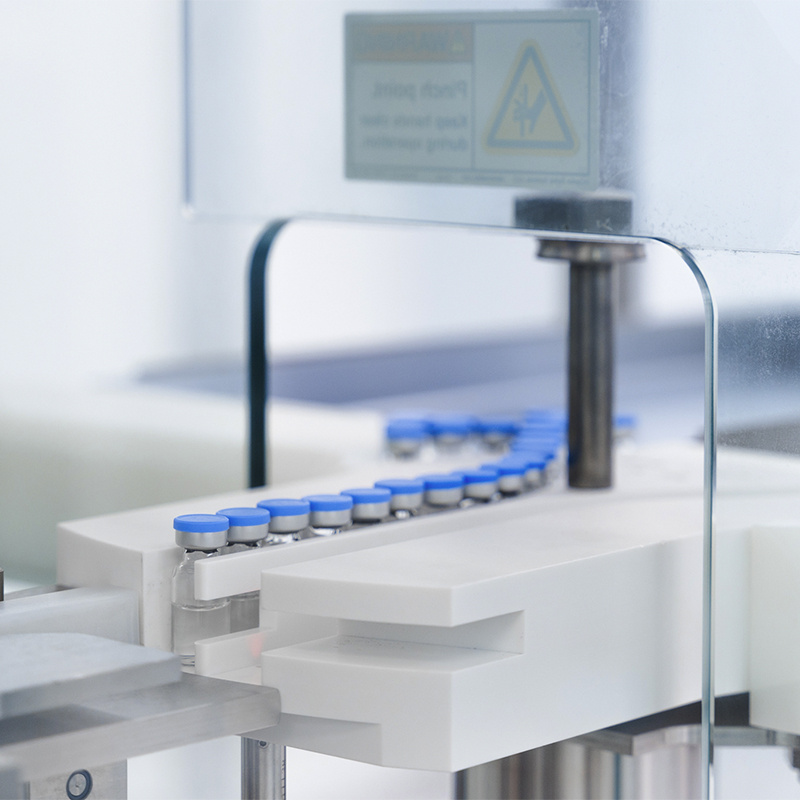
Laboratory site
- 2,500 sq. ft. facility
- Method development and validations
- Analytical QC release
- Microbiological QC release
- ICH stability
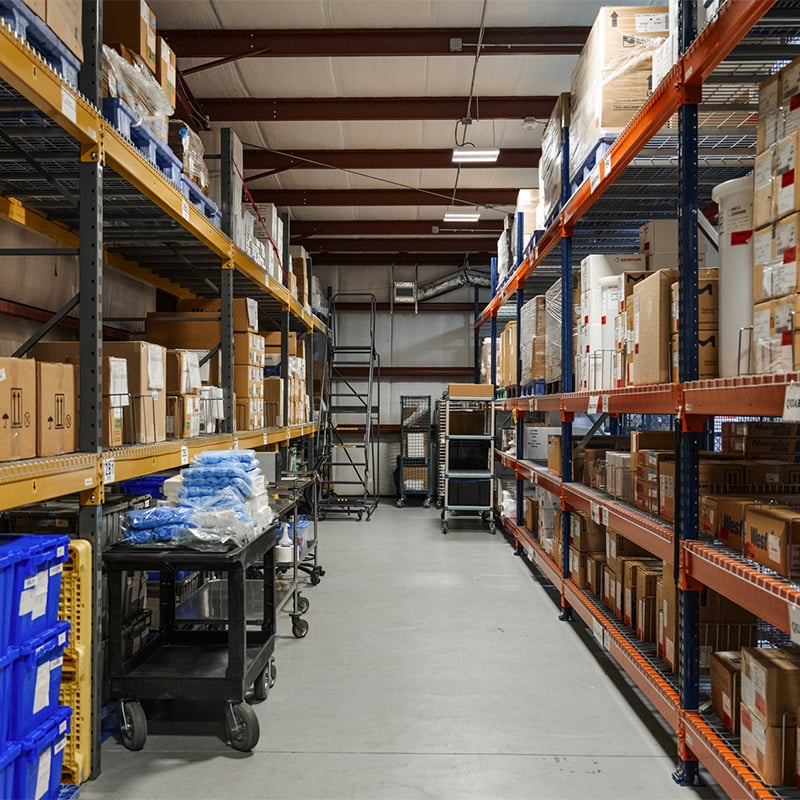
Packaging and warehouse site
- 10,800 sq. ft. expansion
- Raw material and component warehousing
- Finished product warehousing
- Inspection and packaging
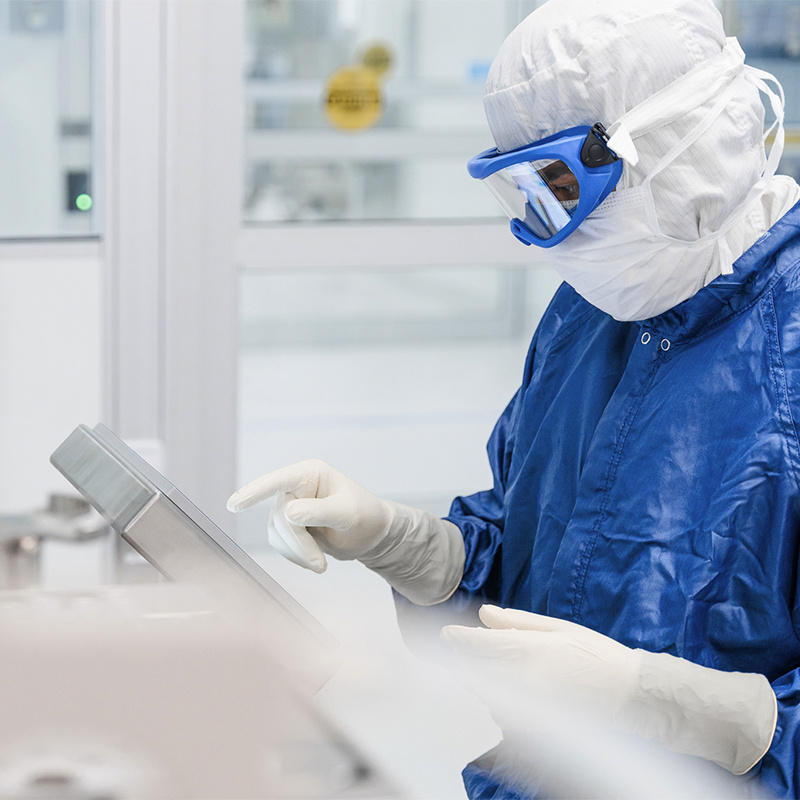
Clean rooms
We use quality by design (QbD) engineering and physical barriers to enhance critical process segregation for improved safety, cleanliness, and material flow. The result is a cleanroom structure that is easier to control, prevents mixups, and increases throughput.
- 10,000 sq. ft. of ISO 5/7 cleanrooms
- Dedicated gown in/out areas
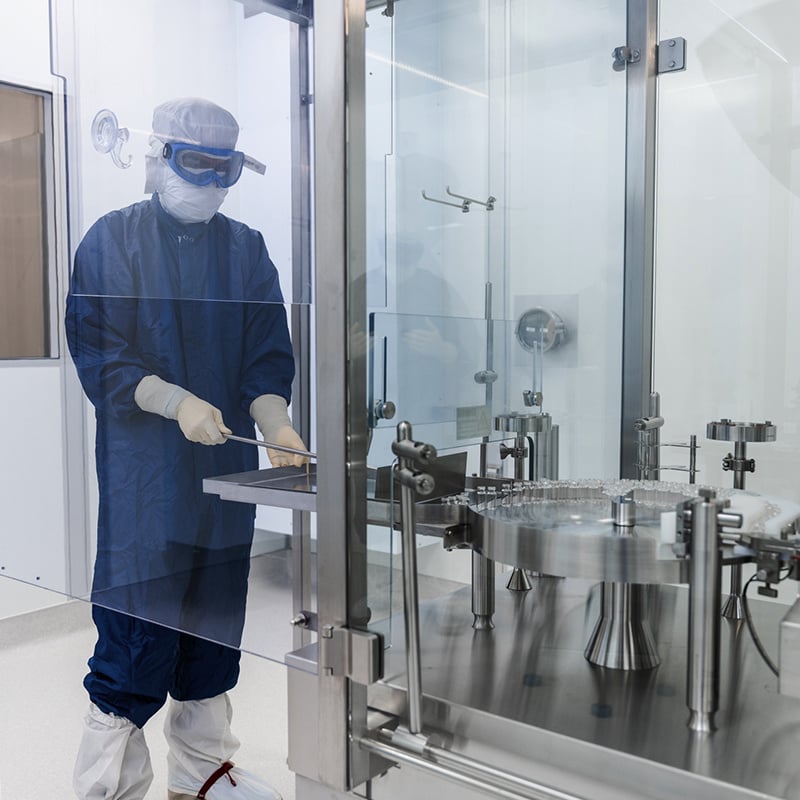
State-of-the-art equipment
With all new equipment manufactured in 2017 or later, the latest technologies and efficiencies are built into every system.
- Optima syringe filling line
- Bosch vial filling line
- Automated mixing vessels
- Fedegari autoclave
- Fedegari dry heat oven
- Girton CIP/SIP
- Girton parts washer
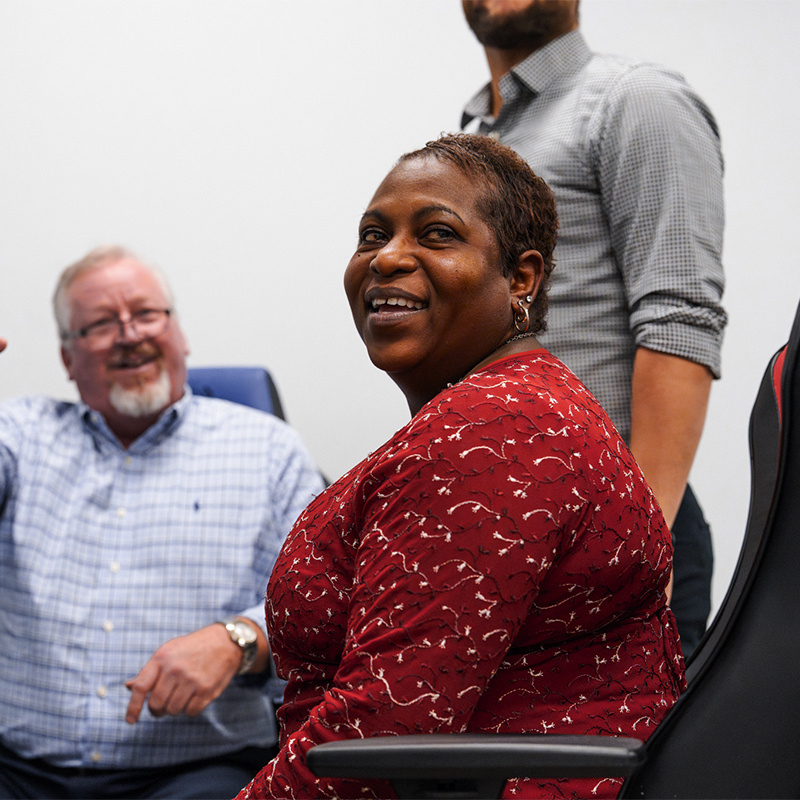